- Cooling capacity0.3kW~3kW
- Heating Power2kW~3kW
- Power range2.9kW~5kW
- Medium accuracy±0.5℃
- Material accuracy±1℃
- RefrigerantR404A/R507C
- Weight55KG~85KG
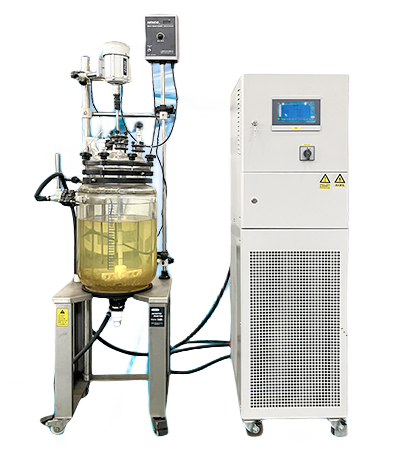
Dynamic Cooling Heating System
Fully enclosed system, single medium completes refrigeration and heating
Control temperature
-120~350℃
Temperature Accuracy
±0.5℃
Configuration Details
Model | SUNDI-320 | SUNDI-420W | SUNDI-430W | |
Temp. range | -30℃~180℃ | -40℃~180℃ | -40℃~200℃ | |
Control Mode | Feedback PID + Our special dynamic control calculation, PLC controller | |||
Temp. control | Process temp. control and jacket temp. control model | |||
Temp. difference | Set or control the temperature difference between jacket oil and raw material process | |||
Program Editor | 5 programs, each program can edit 40 steps | |||
Communication Portocol | MODBUS RTU Protocol,RS485 interface | |||
Material temp. feedback | PT100 | |||
Temp. feedback | The temp. of three points: the inlet and outlet of equipment,reactor material temp.(external temp. sensor) | |||
Medium temp. acccuracy | ±0.5℃ | |||
Material temp. accuracy | ±1℃ | |||
Heating power | 2KW | 2KW | 3KW | |
Cooling capacity | 180℃ | 1.5kW | 1.8kW | 3kW |
50℃ | 1.5kW | 1.8kW | 3kW | |
0℃ | 1.5kW | 1.8kW | 3kW | |
-5℃ | 0.9kW | 1.2kW | 2kW | |
-20℃ | 0.6kW | 1kW | 1.5kW | |
-35℃ | 0.3kW | 0.5kW | ||
Circulation pump | Max10L/min 0.8bar |
Max10L/min 0.8bar |
Max20L/min 2bar |
|
Compressor | Secop/French Tecumseh | Secop/French TecumsehSecop/French Tecumseh | ||
Expansion valve | Electronic expansion valve | |||
Evaporator | Plate heat exchanger | |||
Operation Panel | 7-inch touch screen,show temp curve\EXCEL data output | |||
Safety protection | Self-diagnosis function; freezer overload protection; high pressure switch, overload relay,thermal protection device, liquid low level protection, high temperature protection and temperature fault protection. | |||
Closed circulation system | The whole system is full closed circulation, there is no oil mist at high temperature and no water vapor at low temperature, pressure do not rise up when system is running. The system will supply oil automatically at low temperature. | |||
Refrigerant | R404A/R507C, | |||
Connection size | ZG1/2 | ZG1/2 | ZG1/2 | |
Water-cooled type W(cooling water@20℃) | 800L/H 1.5bar~4bar |
8000L/H 1.5bar~4bar |
||
Dimension(mm) | 350*560*750 | 400*700*1300 | 470*700*1300 | |
Positive ex-proof size(mm) | 700*750*1215 | 700*750*1215 | ||
Weight | 55kg | 60kg | 85kg | |
Power | AC 220V 50HZ 2.9kW(max) | AC 220V 50HZ 3.3kW(max) | AC380V 50HZ 5kW(max) | |
Case material | Cold rolled sheet spray molding (standard color 7035) | |||
Optional | positive pressure ex-proof system add PEX at the end | |||
Optional | Optional Ethernet interface, configure the computer operating software | |||
Optional | Optional outside touch screen display controller(separated),the communication line distance is 10 meter. | |||
Optional Power | Optional power 100V 50HZ single-phase,110V 60HZ single-phase, 230V 60HZ single-phase, 220V 60HZ three-phase,440V~460V 60HZ three-phase | |||
Optional | The sundi series can be selected within the heating power of 25kW. The temperature control accuracy of the medium is ±0.1°C, and the temperature control accuracy of the material is ±0.1°C. |
Description
Ultra-high Temperature Cooling Technology Can Directly Cool Down From 300℃ High Temperature. Because only the heat transfer medium in the expansion chamber is in contact with the oxygen in the air (and the temperature of the expansion tank is between normal temperature and 60℃), which can reduce the heat transfer medium. The risk of oxidizing and absorbing moisture from the air. No high-temperature heat medium evaporates at high temperature, and continuous control can be achieved with -80℃ to 190℃, -70℃ to 220℃, -88℃ to 170℃, -55℃ to 250℃, and -30℃ to 300℃ without pressurization temperature.
principle
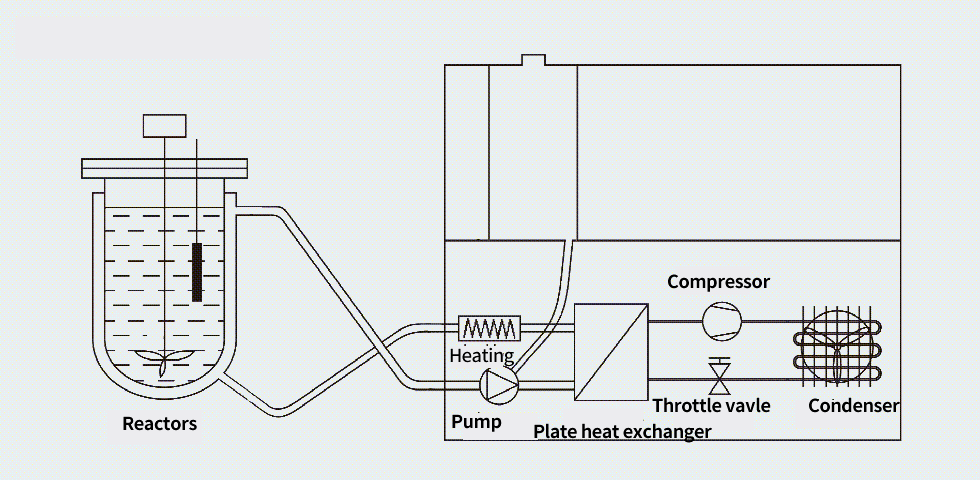
Adopting a fully enclosed pipeline design and an efficient plate heat exchanger, it reduces the demand for heat transfer fluid while improving the system’s heat utilization efficiency, achieving rapid temperature rise and fall.
Because only the thermal conductive medium inside the expansion chamber comes into contact with oxygen in the air, it can reduce the risk of oxidation and absorption of moisture in the air. At high temperatures, no thermal conductive medium evaporates, and there is no need to replace the thermal conductive medium. Moreover, continuous temperature control in multiple temperature ranges can be achieved without the need for pressure.
Applications
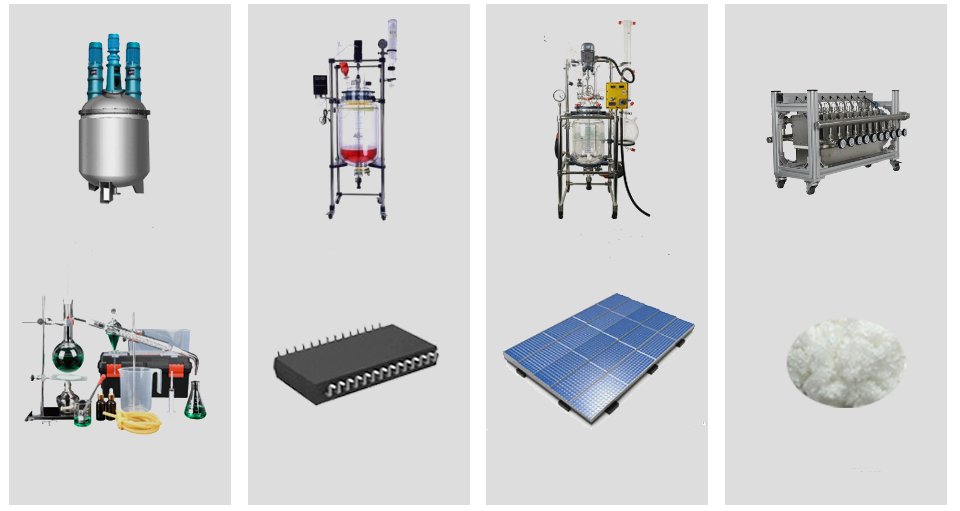
Application: Various Reactors (Microchannels, Glass, Jacketed Reactors, etc.), Distillation or Extraction System, Laboratory, University, Research Institute, Aerospace, Automotive Industry, Semiconductor and Electrical Test, Chemical, Pharmaceutical, Petrochemical, Biochemical, Medical, Hospital, R&D Workshop, Aerospace, Biological and Other Industries.
For pilot production/experimental instruments
Provide temperature support to improve production efficiency
Equipment details
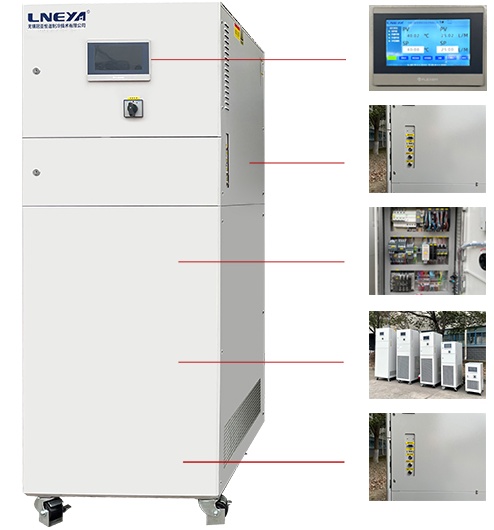
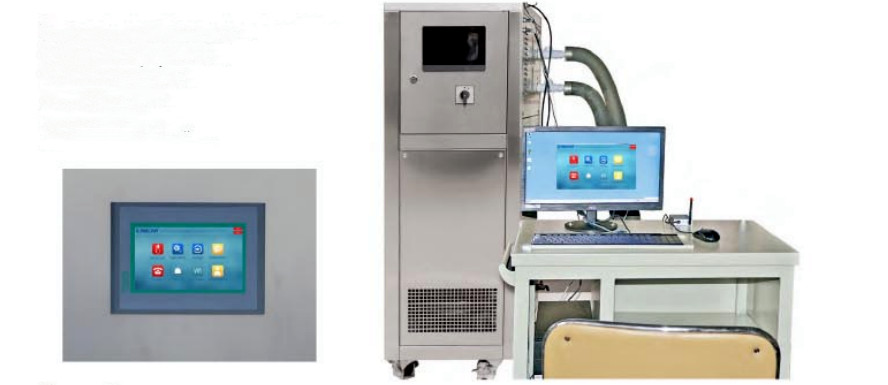
It can be integrated into the device system of the client. Remote data download.
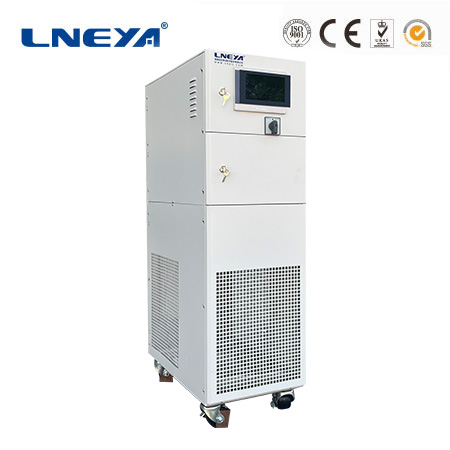
recommend products
SUNDI Z Frequency Conversion Series
WHATSAPP WECHAT Ultra high temperature cooling technology can directly cool from a high temperature of 300℃[because only the heat transfer medium in the expansion…
SUNDI -10℃~150℃
Fully enclosed system, single medium completes refrigeration and heating -120~350℃ ±0.5℃ AC 380V 50HZ 8kW max Ultra high temperature cooling technology can directly cool from a hi…
SUNDI -80℃~250℃
● Working temperatures from -120°C to +350°C ● Previously unachievable performance ●Intelligent temperature control ● Maximum process stability and reproducibility ● Adop plate heat exchager, Pipeline heating, the fastest he…
SUNDI -25℃~200℃
Fully enclosed system, single medium completes refrigeration and heating -120~350℃ ±0.5℃ ● Working temperatures from -120°C to +350°C ● Previously unachievable performance ●Intelligent temperature control…
SUNDI -25℃~300℃
● Working temperatures from -120°C to +350°C● Previously unachievable performance●Intelligent temperature control● Maximum process stability and reproducibility● Adop plate heat exchager, Pipeline heating, the fastest heating a…
SUNDI -45℃~250℃
● Working temperatures from -120°C to +350°C ● Previously unachievable performance ●Intelligent temperature control ● Maximum process stability and reproducibility ● Adop plate heat exchager, Pipeline heating, the fastest heat…
SUNDI -60℃~250℃
Ultra high temperature cooling technology can directly cool from a high temperature of 300℃[because only the heat transfer medium in the expansion chamber contacts with ox…
SUNDI -80℃~250℃
● Working temperatures from -120°C to +350°C● Previously unachievable performance●Intelligent temperature control● Maximum process stability and reproducibility● Adop plate heat exchager, Pipeline heating, the fastest heating…
loading…
已经是到最后一篇内容了!