Chiller unit for power limit testing of new energy batteries
The working principle of power limiting mode: When the system detects low battery level or high temperature, it will automatically enter power limiting mode to avoid excessive use of the battery and protect the battery and motor. Testing method: Evaluate the performance and stability of the battery in limited power mode by simulating these extreme conditions.
The main reason for requiring a chiller for power limit testing of new energy batteries is to ensure temperature control of the battery during high load operation.
In the testing of new energy batteries, the role of the chiller is mainly reflected in the following aspects:
Temperature control and heat dissipation: Batteries generate a large amount of heat during high load operation. Excessive temperature not only affects the performance of the battery, but also shortens its service life. The chiller provides a stable cooling water flow to help the battery dissipate heat in a timely manner, ensuring that the temperature of the battery is maintained within a suitable range during operation.
Simulate real working conditions: New energy batteries will have different temperature requirements in different working environments and conditions. The chiller can simulate various extreme temperature environments, such as high and low temperatures, to help test the performance of batteries at different temperatures. For example, a chiller can provide precise temperature control support for testing the starting performance of a battery in extremely cold environments or its ability to operate continuously under high temperature conditions.
Improving testing accuracy: Accurate temperature control is crucial for battery performance testing. The chiller can maintain a constant cooling temperature to avoid testing data errors caused by temperature fluctuations. By conducting temperature control tests on different operating states of the battery, researchers can more accurately evaluate key performance indicators such as efficiency, durability, and thermal stability of the battery.
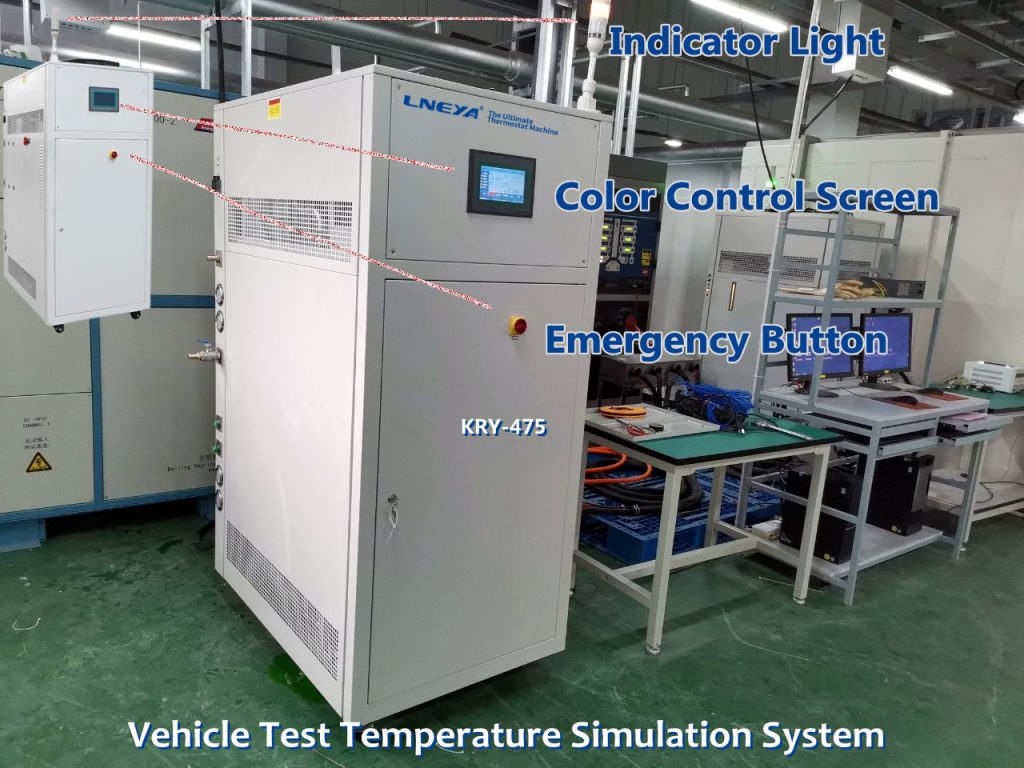
LNEYA chillers are typically equipped with high-precision temperature sensors and controllers that can monitor the temperature of the coolant in real time and automatically adjust the operating status of the refrigeration system based on the set temperature value, ensuring that the temperature of the coolant remains within the set range. Equipped with advanced temperature control technology, it can achieve temperature control accuracy of ± 0.1 ℃ or even higher, meeting the strict requirements for temperature accuracy in lithium battery testing. It has multiple safety protection functions, such as overvoltage protection, overcurrent protection, overheating protection, antifreeze protection, etc., to ensure the safety of equipment and testing personnel.
Select a chiller with appropriate cooling capacity based on the power and heat dissipation requirements of lithium battery testing. Insufficient cooling capacity cannot meet the testing requirements, while excessive cooling capacity can result in energy waste and increased costs. Determine the required temperature range to ensure that the chiller can provide low-temperature coolant that meets the requirements of lithium battery testing. In terms of flow and pressure, it is necessary to consider the requirements of lithium battery testing equipment for coolant flow and pressure, and choose a suitable chiller model.
Recommended products
- MORE
KRYZ Frequency Conversion Series
- 参数标题参数内容
Rated test conditions: dry bulb temperature 20℃; wet bulb temperature 16℃. Inlet water temperature 20℃; outlet water temperature 25℃. The data in this table is for reference only. Please refer to the …
- MORE
KRY Direct Cooling Heating Series
- 参数标题参数内容
Rated test conditions: dry bulb temperature 20℃; wet bulb temperature 16℃. Inlet water temperature 20℃; outlet water temperature 25℃. The data in this table is for reference only. Please refer to the unit name…
- MORE
Oil Cooling Chiller KRYO Series
- 参数标题参数内容
For the power battery charging management, the precision temperature control device for testing the permanent magnet synchronous motor, the switched reluctance motor, the asynchronous…
- MORE
KRY -40℃~+100℃ (1to6)
- 参数标题参数内容
The components are cooled and heated internally through ethylene glycol aqueous solution for testing -40 ° C~100 ° C (expandable to 150 ° C) For the power battery charging management, the precision …
- MORE
KRY -40℃~+100℃ (1to1)
- 参数标题参数内容
Refrigeration, heating, temperature control, flow control Connect the tested object to a testing platform adapterThe components are cooled and heated internally through ethylene glycol aqueous solution for testing. …
- MORE
KRY -40℃~+100℃ (1to2)
- 参数标题参数内容
Temperature range is -40℃~+100℃, which can be extended to +135℃ according to the actual situation, and the temperature control accuracy is plus or minus 0.5℃. Theequipment can control the flow and pressure independently while c…
- MORE
KRY -40℃~+100℃ (1to3)
- 参数标题参数内容
Dimension(A) cm Temperature range is -40℃~+100℃, which can be extended to +135℃ according to the actual situation, and the temperature control accuracy is plus or minus 0.5℃. Theequipment can control the flow and…
- MORE
KRY 0℃~+100℃ (1to2)
- 参数标题参数内容
Temperature range is 0℃~+100℃, which can be extended to +135℃ according to the actual situation, and the temperature control accuracy is plus or minus 0.5℃. The equipment can control the flow and pressure independently …
- MORE
KRY 0℃~+100℃ (1to3)
- 参数标题参数内容
Test temperature of main test items of vehicle electronics: IC test conditions for locomotives: -40℃~125℃, wind blowing, sun exposure, high vibration; Instrument panel operation te…
- MORE
KRY 0℃~+100℃(1&6)
- 参数标题参数内容
Temperature simulation for vehicle quality test: battery life test, fuel injector/motor test bench, airbag test, component test bench, etc. It can simulate the external environmental conditions in the climat…
loading…
已经是到最后一篇内容了!