Laminated Glass Reactor
Double-layer glass reactors are suitable for the reaction of large amounts of liquids. The heating speed is fast and uniform, but the operation is more complicated and requires strict control of temperature and pressure. The interlayer circulates through the cold and heat sources. The interlayer of the glass reactor can provide high-temperature reactions (the highest temperature can reach 300°C); the glass reactor can also do low-temperature reactions (the lowest temperature can reach -80°C); the glass reactor can be evacuated for negative pressure reactions.
The body of the three-layer glass reactor is a double-layer structure. The inner interlayer is connected to the temperature control circulation device, and the temperature of the material in the reactor is adjusted by the circulating liquid; the outer interlayer can be pumped to a negative pressure state to achieve a vacuum insulation function, which can prevent the reactor body from frosting under low temperature conditions and facilitate observation of the reaction conditions in the reactor.
Glass jacket open cover reactor
Special durable mixing shaft seal
Double layer anti-corrosion mixing paddle
Bottom discharge valve with no liquid accumulation and large diameter
Stainless steel frame
Variable frequency over torque protection mixing control
Explosion proof models are optional
Parameters
1 | Reaction kettle body (L) (open cover type) | 10L, 50L,100L,150L |
2 | Maximum discharge diameter(mm) | ∅32 |
3 | Number of kettle cover interfaces | 7 |
4 | Rotating speed(rpm) | 20-400 |
5 | Torque(Ncm) | 390 |
6 | Stirring rod diameter(mm) | ∅20 |
7 | Power supply | 220V,1P,50/60Hz |
8 | Overall size(cm) | 110x60x230H |
Function Configuration
1 | Frequency | ● |
2 | Digital Display | ● |
3 | PTFE combined seal | ● |
4 | PTFE direct discharge valve | ○ |
5 | PTFE closed discharge valve | ● |
6 | PTFE filling valve | ● |
7 | Dropping system(L) | 5L |
8 | Solid feed port | F80 |
9 | Thermometer | ● |
10 | Vacuum gauge | ● |
11 | Tangential interlayer inlet and outlet | F40-M30x1.5 |
12 | Reflux condensation | ● |
13 | Distillation-layering-collection | ○ (10L) |
14 | Distillation collection * | ○ |
15 | Sampling bottle | ○ |
16 | Jacket pressure regulating device * | ○ |
17 | Kettle pressure relief valve * | ○ |
18 | Kettle body spoiler baffle | ○ |
19 | Stainless steel base | ● |
20 | Moving pulley | ● |
21 | Explosion-proof/Pneumatic Modification* | ○ |
22 | Overcurrent protection | ● |
23 | Spark-free electronic control system | ○ |
Symbol meaning:/- None, ● – Equipped, ○ – Optional (* – This optional function must be assembled during factory production and cannot be separately equipped)
Note: The specific parameters of the associated models or customized models may differ from those of the standard models. You can contact us for specific inquiries.
Product Description
Kettle cover configuration (above 10L)
● Feeding valve—clean feeding throughout the process, no pollution
● Thermometer—directly measures material temperature
● Condenser—ball mouth connection, easy to install and shock-absorbing
● The kettle cover interface is fully upgraded to flange connection, equipped with SENCO quick-release flange clamping ring. The interface is not bitten and the glass is not damaged.
● The main bottle has no cone mouth, eliminating the damage to the bottle body caused by the cone mouth biting
PTFE bottom side discharge valve:
No dead angle, no liquid accumulation, maximum discharge diameter Ø20~32mm. The pre-tightened structure can effectively reduce the risk of accidental damage to the reactor body due to excessive top rotation of the bottom valve, which is particularly important for pilot reactors.
Quick-release flange clamping ring:
It can provide a new experience of flange connection with high airtightness, high corrosion resistance, and easy loading and unloading.
PTFE feeding valve:
The latest structure and material design, high clean feeding throughout the process, high corrosion resistance and wear resistance.
Mirror flange processing technology:
SENCO flange uses fine cold grinding and polishing technology to ensure the airtightness of static interface connection.

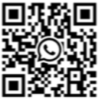
Email: sales@cnzlj.com
WhatsApp: 086 13912479193
Related recommendations
-
Molecular distillation (Short range distillation)
1793Short range distillation (molecular distillation) is a new separation technology that can solve problems that conventional distillation techniques cannot solve. It can achieve liquid-liquid separation at temperatures far below the boilin...
View details -
Rotary Evaporator 1-50L
1632Small desktop rotary Evaporator 1L~5L Pilot and ground mounted rotary evaporators 10L~50L Rotary evaporator, also known as rotary evaporator. It consists of motor, distillation flask, heating pot, condenser and other parts. It is...
View details -
Molecular distillation (Short range distillation)
1793Short range distillation (molecular distillation) is a new separation technology that can solve problems that conventional distillation techniques cannot solve. It can achieve liquid-liquid separation at temperatures far below the boilin...
View details -
Rotary Evaporator 1-50L
1632Small desktop rotary Evaporator 1L~5L Pilot and ground mounted rotary evaporators 10L~50L Rotary evaporator, also known as rotary evaporator. It consists of motor, distillation flask, heating pot, condenser and other parts. It is...
View details -
ST series
1804ST-25W ST-38W ST-60W ST-100W ST-200W ST-300W Steam pressure 4~6bar Hot water temperature range RT+10℃~135℃ Temperature control accuracy ±1℃ ±1℃ ±1℃ ±1℃ ±1℃ ±1℃ Heat transfer capacity max 25kW 38kW 60kW 100kW 200kW 300kW Steam...
View details -
AET Series
3526Suitable for IC testing of all kinds of semiconductor chips,flash memory Flash/EMMC, PCB circuit boards, opticalcommunications,electronic industries, etc. Rated test conditions: dry bulb temperature 20℃; wet...
View details
Submit for consultation
We will reply to you within 24 hours