What are the common connection methods for industrial chillers?
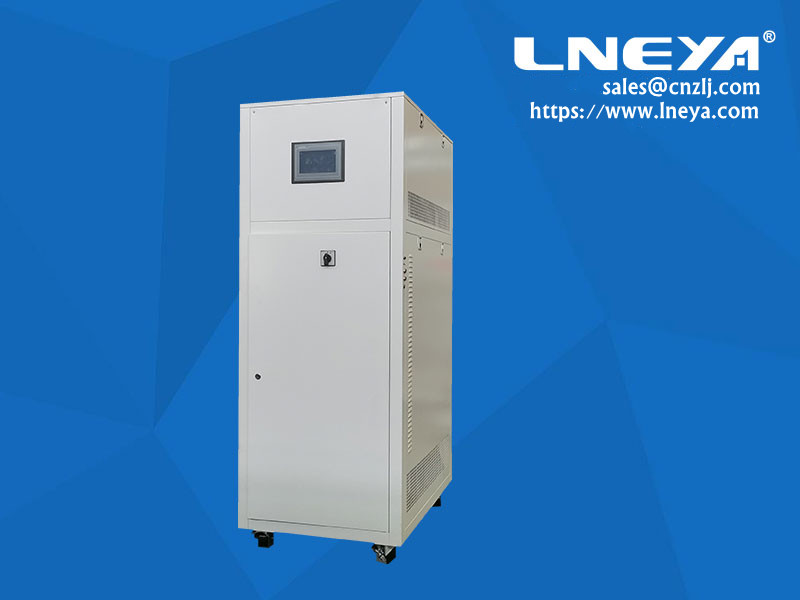
There are several connection methods for industrial chillers, which are suitable for pipe connection under different conditions.
First, welding connection
Welding is the most important and widely used connection method in pipeline engineering. Welding connection is a direct and fixed connection between pipe sections; it is commonly used in large-diameter steel pipes, high-temperature and high-pressure pipes, overhead steel pipes, buried or laid in trenches, etc. . It has obvious advantages such as high strength and tightness of the interface, omission of fillers and joint accessories, fast construction speed, and no limitation of pipe diameter; but it also has the advantages of non-disassembly, complex interface operation technology, and welding equipment and welder cooperation during construction. And other shortcomings.
Second, threaded connection
Threaded connection (also called threaded connection), it is suitable for pipes with small working pressure and small nominal diameter (dn≤32mm), as well as the connection of pipes with threaded valves, instruments, and equipment. When connecting, the joint should be smeared with filler prepared by lead oxide and glycerin, and evenly spread on the thread of the pipe thread (do not apply in the valve), or use PTFE plastic tape as the filler. The filler shall not protrude into the pipe to avoid reducing the pipe. On the end face, it is strictly forbidden to replace the filler with white painted hemp wire, and the wire connection must be tightened once, and shall not be returned or loosened.
Third, flange connection
Flange connection is to add gaskets (materials) to a pair of flange plates fixed on two pipe fittings, and then tighten them with bolts to connect them into a detachable whole. It has high connection strength, good sealing performance, convenient disassembly, and standardization of production. Therefore, it is widely used in equipment connections between pipes and flanged pipe fittings or flange interfaces, pipes and flange valves, and pipes. The location that needs to be disassembled and overhauled. During installation, a rubber plate gasket with a thickness of 4mm should be placed in the notch. The gasket shall not have uneven thickness, bevel or notch.
Summarize
We at LNEYA will make a specific analysis according to the customer’s specific working conditions. If you have equipment requirements or equipment problems, please contact us sales@lneya.com
Related recommendations
-
Discrimination of power battery integration test system
1428Using the degree of superheat to judge whether the opening degree of the integrated test system of the power battery is appropriate, and using a thermometer to measure the difference between the temperature of the return pipe and the evaporating t...
View details -
The importance of temperature cycle control heating and cooling in the production of API
1286China has become the world's largest supply market for APIs. Most of the APIs and intermediates required by foreign manufacturers are purchased in my country. The drug outsourcing process of most of its preparation products, the production process...
View details -
Temperature control during new energy vehicle battery test
1122With the continuous implementation of energy saving and emission reduction policies, new energy power batteries are also continuously encouraged to develop, and liquid cooling systems have become an inevitable trend for new energy vehicles. The or...
View details -
Rapid temperature change test chamber temperature control instructions
1073The selection of the humidity range of the rapid temperature change test chamber should be noted that the corresponding temperature range should be indicated after the humidity index or the dew point temperature should be given. Because relative h...
View details