What Are The Chiller Safety Checklist Essential Steps ?
Still worried about your chiller safety? Want to keep your industrial chiller running at peak cooling performance? This blog post addresses your concerns in detail and provides a comprehensive safety maintenance checklist for your chiller. Keep reading to learn more!
Why Chiller Safety Matters
Safety in production has always been a top priority for both society and businesses. It is directly tied to the protection of human life and property. In daily operations, ensuring safe production is not only a legal requirement but also a fundamental pillar for long-term, stable business growth. Regardless of the industry, any activity involving production must embed safety awareness into every step of the process, backed by strict regulations and effective enforcement.
In the industrial sector in particular, chillers play a crucial role as one of the key pieces of equipment. Industrial chillers provide stable temperature control essential to many complex production processes, helping maintain the efficiency and reliability of entire production lines. However, the chiller safety must not be overlooked. Malfunctions or improper operation can lead not only to costly production downtime but also to serious safety hazards.
Therefore, while businesses prioritize overall workplace safety, they must also pay close attention to the safe operation and maintenance of their chillers. Regular inspections and maintenance are essential to keeping the equipment in optimal condition. This approach not only protects employees but also serves the long-term interests and sustainability of the business.
Pre-Operation Safety Checks: What to Inspect Before Startup
Before starting the chiller, you should check the following items:
Refrigerant Safety: Handling, Storage, and Leak Prevention
- Check for Refrigerant Leaks:
Inspect the chiller system for any signs of refrigerant leakage. Leaks can reduce cooling efficiency and may damage the system if not addressed promptly. - Check the Refrigerant Level:
Make sure the refrigerant level stays within the recommended operating range. If it is insufficient, refill it to the appropriate level to maintain optimal performance.
Electrical System Safety: Lockout/Tagout and Circuit Checks
Ensure that the working voltage is stable. If the voltage is unstable, installing a voltage stabilizer is recommended to ensure consistent and safe operation.
The electrical system of a chiller is particularly susceptible to power phase sequence faults. These issues are typically caused by incorrect wiring, unbalanced power phases, or internal circuit faults within the equipment.
Steps for troubleshooting power phase issues:
- Inspect Power Line Connections:
First, check that the power lines are connected correctly—this includes the live wires, neutral, and ground. Ensure all wires are securely fastened and properly connected, with no loose or incorrect connections. - Check Power Phase Balance:
Use a phase sequence detector to check and confirm the correct balance of the power supply. Ensure that the voltage and current are balanced across all phases. - Inspect Internal Circuits of the Chiller:
Remove the chiller’s outer casing and examine the internal wiring carefully. Look for signs of burning, loose connections, or other abnormalities.
Pressure Controls and Relief Valve Inspections
- Check the Chiller’s Pressure Gauge:
The pressure gauge displays the operating pressure of both the compressor and the refrigerant. Regular monitoring helps identify any abnormalities at an early stage. - Ensure the Pressure Sensor Is Functioning Properly:
Pressure anomalies may sometimes be caused by a faulty pressure sensor. Make sure the sensor is operating correctly to avoid inaccurate readings. - Inspect the Expansion Valve Opening:
Make sure the expansion (throttle) valve is correctly adjusted to the appropriate opening. An incorrect setting can affect the refrigerant flow and cooling performance. - Check the Condenser for Scale or Blockages:
Inspect the condenser for signs of scale buildup or blockages. These can reduce heat exchange efficiency and lead to increased system pressure or reduced cooling capacity.
Ensuring Proper Flow and Temperature Monitoring
- Check Cooling Water Flow Rate:
If the cooling water flow rate does not meet the rated requirement, the pressure difference between the inlet and outlet will decrease, while the temperature difference will increase—both of which can negatively impact performance. - Verify Temperature Settings:
Set the temperature reasonably. If the set temperature is too low, it can reduce the chiller’s cooling efficiency. As a general guideline, set the water temperature slightly below the required process temperature. Adjust settings based on actual needs. - Inspect the Temperature Sensor:
Ensure the temperature sensor is functioning correctly, as faulty readings can lead to improper system operation.
Emergency Shutdown Procedures and Alarm Testing
- Inspect the Chiller’s Alarm System:
Take LNEYA chillers as an example: they are equipped with self-diagnostic features and multiple safety protections, such as overload protection, overload relays, and thermal protection devices. These built-in systems help identify issues early and ensure safe operation. - Check the Emergency Stop Button:
Confirm that the chiller’s emergency stop button is working correctly. In the event of an emergency, pressing this button will immediately shut down the chiller, helping to minimize potential losses in the production process.
Chiller Room Safety: Layout, Ventilation, and Access Control
- Inspect the Interior of the Chiller:
Check all internal components to ensure that there are no loose parts. Make sure all connections are secure and properly fastened to prevent operational issues. - Inspect the Chiller’s External Environment:
Pay attention to the surrounding environment. For example, in the case of air-cooled chillers, maintaining good ventilation around the unit is essential for efficient heat dissipation and stable operation.
During operation, chillers can generate high temperatures. Therefore, the unit should be placed away from flammable and explosive materials to avoid potential hazards. Additionally, environments with high radiation levels can negatively impact the chiller’s performance and lifespan.
It is recommended to install the chiller in a well-lit, bright area with stable environmental conditions to ensure safe and efficient operation.
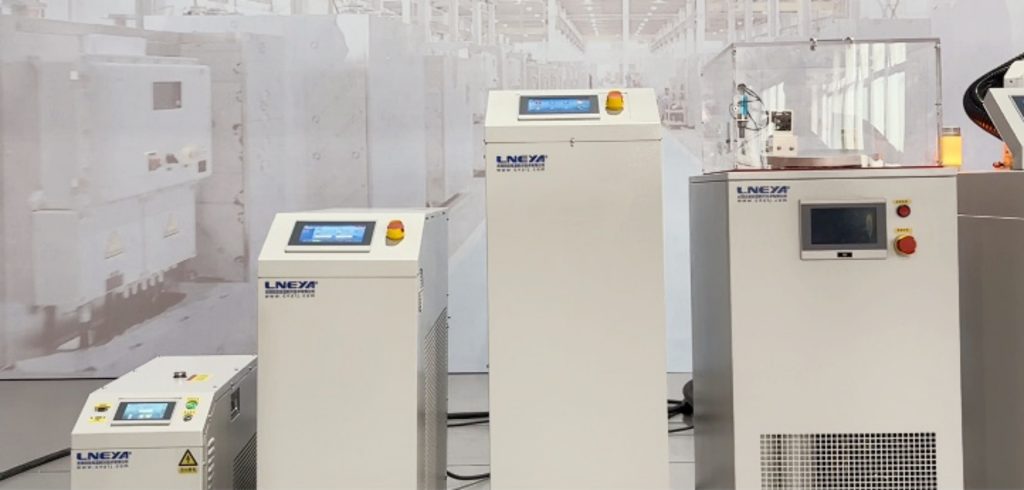
Daily, Weekly, and Monthly Safety Maintenance Tasks
Regular Inspection
Chillers require regular inspections that cover all major systems, including the refrigeration system, electrical system, and water system. When inspecting a chiller, pay attention to the following key areas:
- Refrigeration System:
This is the core of the chiller. Regularly check the refrigerant charge level, inspect for leaks in the refrigerant lines, and ensure the compressor is operating normally. - Electrical System:
Since the electrical system powers the chiller, it should be inspected regularly to ensure reliable operation. Look for signs of aging in the power cables and verify that all electrical components are functioning properly. - Water System:
This system is responsible for cooling. Inspect the cooling water pipes for blockages and check for excessive scale buildup, which can reduce efficiency.
Routine Cleaning
Routine cleaning is crucial to maintaining your chiller’s efficiency and longevity. This includes cleaning the chiller’s exterior, cooling water pipelines, and refrigeration system. When cleaning the chiller, be sure to follow these guidelines:
- Chiller Surface Cleaning:
Keep the exterior of the chiller clean to prevent dust and debris from entering the internal components. - Cooling Water Pipeline Cleaning:
Regularly flush the cooling water pipelines to prevent scale buildup and blockages caused by impurities. - Refrigeration System Cleaning:
Regularly clean the refrigeration system to prevent refrigerant residue or degradation, as these can negatively impact system performance.
Maintenance & Repair
Regular maintenance is essential to ensure the chiller operates efficiently and reliably. This includes replacing wear-prone components and adjusting key equipment settings. When performing maintenance on a chiller, be mindful of the following points:
- Replace Wear-Prone Components:
Components such as refrigerant filters and cooling water pumps should be replaced regularly to maintain proper system function and avoid unexpected breakdowns. - Adjust Equipment Parameters:
Parameters like temperature and pressure should be periodically checked and adjusted to ensure stable operation and achieve optimal cooling performance.
Safe Operation
When operating a chiller, it’s important to follow these safety precautions:
- Follow Operating Procedures:
Always operate the chiller according to the official operating manual. Improper use can result in equipment damage or serious injury. - Inspect Safety Devices:
Regularly check safety features such as emergency stop buttons and safety valves to ensure they are functioning properly and that the chiller can operate safely. - Avoid Overloading:
Never run the chiller under excessive load conditions.Overloading the unit can lead to serious damage and greatly reduce its operational lifespan.
Seasonal Maintenance Tips
How Can You Protect Your Chiller from Freezing in Winter?
During the winter months, chillers are at risk of freezing and damage. So how can you properly protect your equipment?
When the ambient temperature drops below 0°C (32°F) and the chiller is not in use overnight, the first method to prevent freezing is to drain all the water from the chiller’s tank and internal piping. You can refill the system the next day before use.
The second method is to add a proper ratio of ethylene glycol to the chiller’s water tank and piping. The colder the temperature, the higher the concentration of ethylene glycol needed.
As a general guideline:
- At -15°C (5°F), use a 15% ethylene glycol solution.
- At -10°C (14°F), use a 20% to 30% ethylene glycol solution.
What Should You Pay Attention to When Using a Chiller in Hot Summer Weather?
During very high temperatures, the chiller should be placed in a shaded and well-ventilated area. The optimal operating temperature range for a chiller is between 20°C and 30°C (68°F–86°F). It is advisable to maintain the ambient temperature below 40°C (104°F) for efficient performance.
The chiller should not be placed too close to surrounding objects. It is recommended to maintain a minimum clearance of 1.5 meters (approximately 5 feet) at the air outlet and at least 1 meter (approximately 3 feet) at the air inlet.
During periods of peak electricity demand in summer, voltage fluctuations may occur. To ensure stable operation, it is advisable to install a voltage stabilizer or use a power supply with built-in voltage regulation. The stabilizer’s power rating should be at least 1.5 times the chiller’s rated electrical power.
The chiller’s fan provides heat dissipation. Regularly check the fan’s operating condition, and use an air gun to clean dust and debris from the dust filter and the condenser surface. The greater the chiller’s power, the more frequently dust cleaning should be performed.
Training and Documentation: Establishing a Culture of Safety
To ensure chiller safety throughout the production process, we strongly recommend providing systematic training for your operators. The training should cover key areas such as chiller startup and shutdown procedures, operational management, understanding the alarm system, proper actions in the event of a fault, and daily chiller maintenance training best practices.
As an expert in the field of chillers, LNEYA offers comprehensive chiller services, including professional maintenance support. For more information or to request service, please contact us at market@lneya.com — we’re here to help!
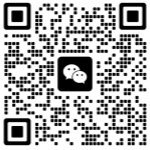
WeChat/Phone
86 18914253067
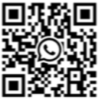
86 13912479193
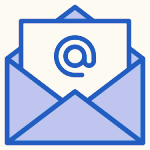
Email Address
sales@cnzlj.com
Recommended chillers
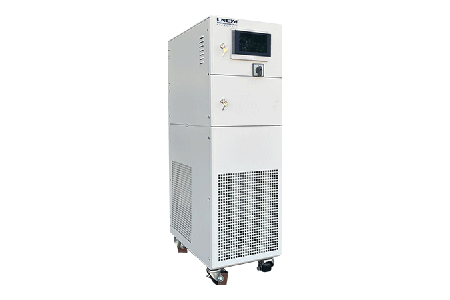
LTZ +5℃-90℃
glycol chillers
Cooling capacity 4kW~20kW
Heating power 3.5kW~15kW
temperature accuracy ±0.3℃
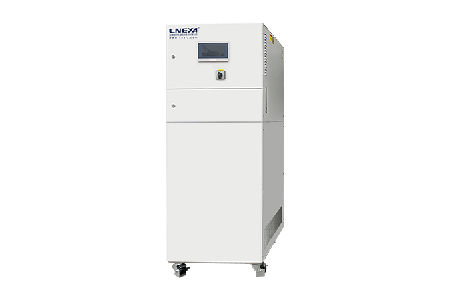
LTZ -40℃~90℃
fluid chillers
Cooling capacity 0.7kW~11.5kW
Heating power 2.5kW~10kW
temperature accuracy ±0.3℃
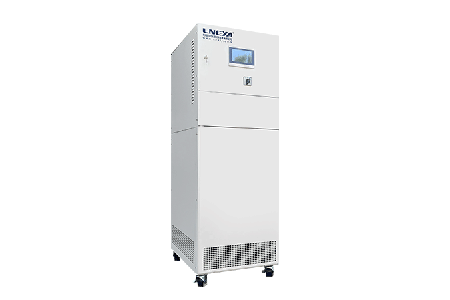
LTZ +5℃~30℃
laboratory chillers
Cooling capacity 23kW~155kW
Circulation Pump MAX 5m³/h~28m³/h 2bar
temperature accuracy ±0.5℃
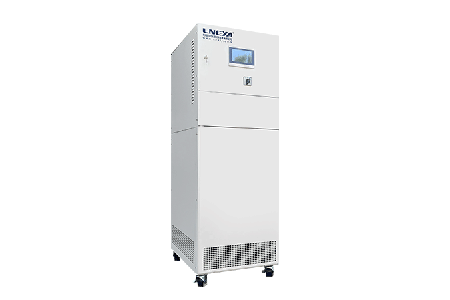
LTZ -25℃~30℃
sub zero chillers
Cooling capacity 7kW~64.5kW
Circulation Pump MAX 2.5m³/h~15m³/h 2bar
temperature accuracy ±0.5℃